- Case Study -
Data Integration for Equitable Distribution
During the COVID-19 pandemic, businesses worldwide faced significant challenges, including shortages of essential supplies. A leading Diagnostic Company encountered disruptions in its supply chain and customer service operations due to stock shortages of critical products. Initially, they relied on manual methods, such as Excel spreadsheets, to manage inventory, pulling data from various applications. However, these manual processes took up a lot of their team’s time and proved insufficient.
Opportunity
Recognizing the inefficiencies of manual inventory management, the Diagnostic Company saw an opportunity to enhance operations through automation and data integration. Partnering with Mindex, they aimed to develop an automated product allocation application to ensure fair supply allocation, save time and resources, and improve transparency in their supply chain operations.
Solution
To address supply-chain shortages and ensure equitable distribution of high-demand products, we developed a comprehensive tool that extracts usage, inventory, and order data from diverse sources, leveraging AWS tools such as Aurora, Redshift, and Lambda. By analyzing this data, we accurately determined both current and predicted usage patterns. With this understanding, the Diagnostic Company can distribute limited-supply products to customers based on how much they typically use compared to overall demand, prioritizing those expected to run out before their next shipment.
How we did it:
Data Migration and Integration:
We employed Database Migration Service (DMS) to seamlessly transfer data across various locations. External Schemas facilitated easy access to product data stored in Aurora. Leveraging federated queries, we efficiently gathered information from diverse sources, including Redshift clusters, and unified it into a cohesive dataset.
Centralized Data Management:
All data was consolidated into a central Redshift database. Materialized views were utilized to calculate product usage and determine restocking requirements accurately.
User-Friendly Access and Automation:
Stakeholders, such as managers or decision-makers, could effortlessly view and interact with the data through intuitive tables. Furthermore, we implemented automated nightly updates using Lambda to ensure data remained precise and current without manual intervention.
Benefits
Accurate Consumption Estimates and Equitable Distribution:
One of the key advantages of the product allocation application was its ability to accurately estimate consumption patterns and distribute supplies fairly.
Adoption by Internal Stakeholders:
The product allocation application was swiftly adopted by internal stakeholders at the Diagnostic Company. It facilitated the allocation of limited product supply, ensuring that resources were distributed efficiently and fairly. Moreover, the tool provided a transparent mechanism to demonstrate to customers that allocation decisions were made in an equitable manner, enhancing trust and credibility.
Efficiency Gains:
This initiative introduced a brand-new tool that was not previously part of the Diagnostic Company's inventory management arsenal. By automating the allocation process, the application saved valuable business time and resources, enabling teams to concentrate on more strategic activities and enhancing overall productivity.
Interested in learning more about how you can leverage your data?
Explore the potential of your data with a complimentary Data Architecture Review by our cloud data team. Led by a Certified AWS Data Architect, this one-hour session dives into your data pipeline's core elements: Data Ingestion, Storage, and Analytics, including AI/ML and Business Intelligence. Our goal is to uncover challenges, identify opportunities, and outline a roadmap for your data strategy.
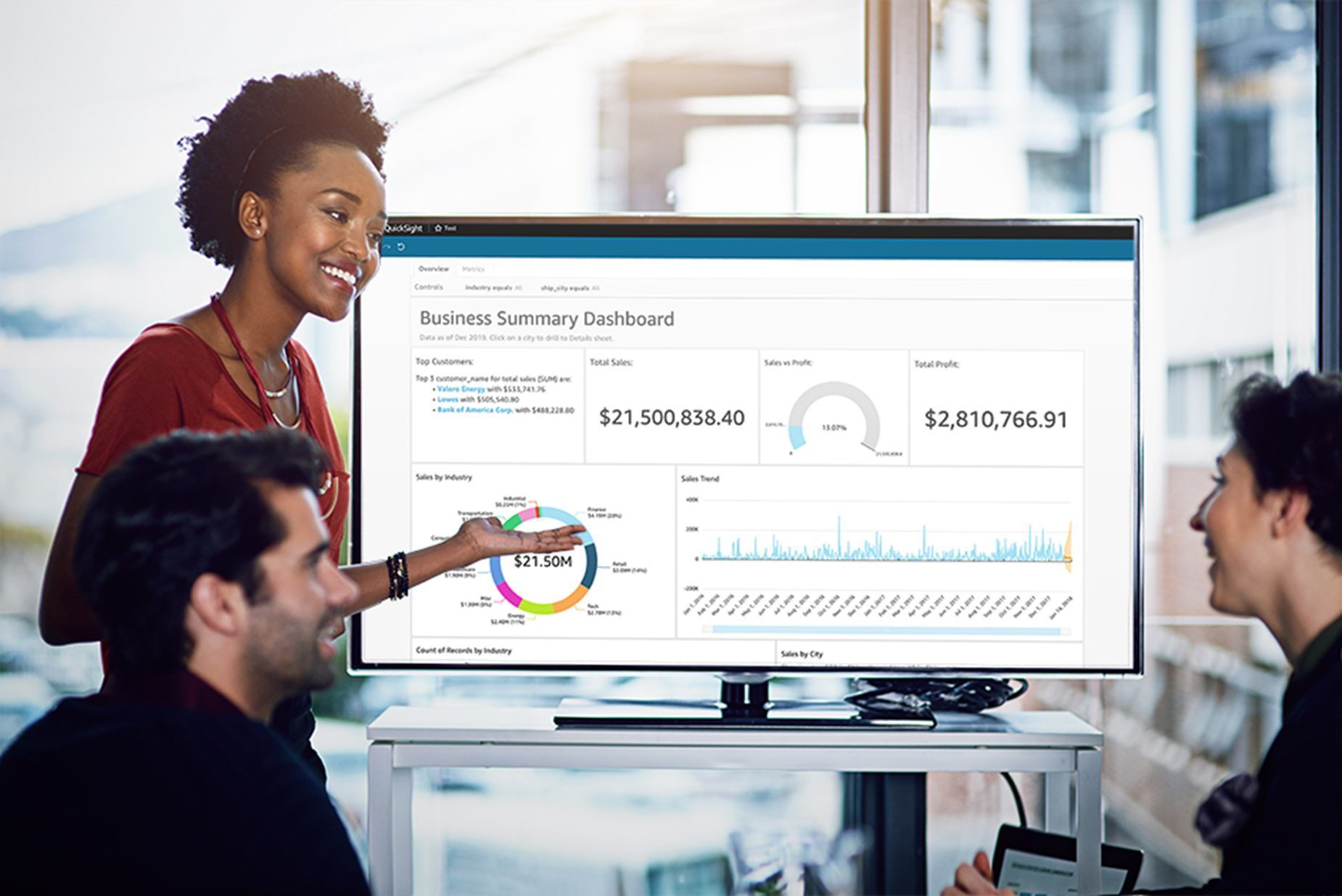